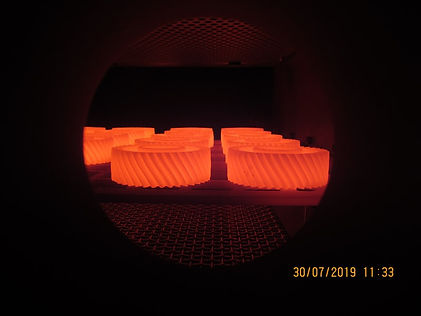
About TOPGEAR
Motivation
As CO2 is the most important GHG and 23% of the CO2 emissions are related to transportation, the EU established a series of successive CO2 emission targets for new vehicles.
The advantages of Hybrid Electric Vehicles (HEV) and, especially, Electric Vehicles (EV) make them the fastest solution to reduce the emissions caused by road transportation.
​
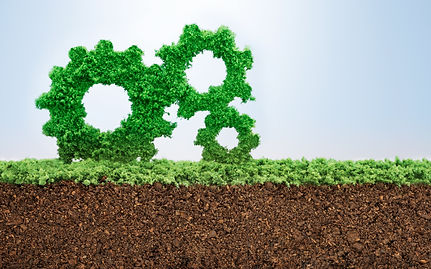
The TOPGEAR project

Starting date
01.08.2021
until 31.01.2025

Duration
42 months

Funded under
Research Fund for Coal and Steel RFCS-RPJ
EC Funding: 1.17 M€
Challenge

As in HEV/EV, the speed of the electric motor is much higher than that of classical internal combustion engines (ICE), the rotating speed of the transmission gears in these eco-friendly cars is also notably higher (8,000 rpm vs 4,000 rpm), having to withstand similar torque to not diminish their performance.
These more stringent working conditions have provoked an augmentation of fatigue failures in gears and the appearance of new failure modes such as scuffing.
Scope and Approach
The new generation of gears for HEV/EV are expected to work at rotating speeds of about 15,000 rpm, this means to double the speed reached in actual HEV/EV and to triple that of ICE cars. Besides, torque must be kept in current values to not affect the in-service performance.
The main aim of the TOPGEAR project is to develop a new manufacturing route, combining new steel solutions and surface hardening treatments, in order to allow the production of gears capable of working at 15,000 rpm without suffering relevant fatigue and scuffing problems.

Solutions and Benefits
_JPG.jpg)
The targeted low temperature surface hardening processes (nitriding and nitrocarburizing) and the new carburizing and quenching process with single-layer-treatment will minimize teeth distortions, This simplification of the finishing operation leads to notable economic savings.
​
The use of F-P microalloyed steels for nitriding/
nitrocarburizing will avoid Q&T, an expensive and pollutant heat treatment, leading to a simplification of the manufacturing process. Furthermore, the machining costs will be reduced thanks to the better machinability of the F-P compared to that of the martensite.